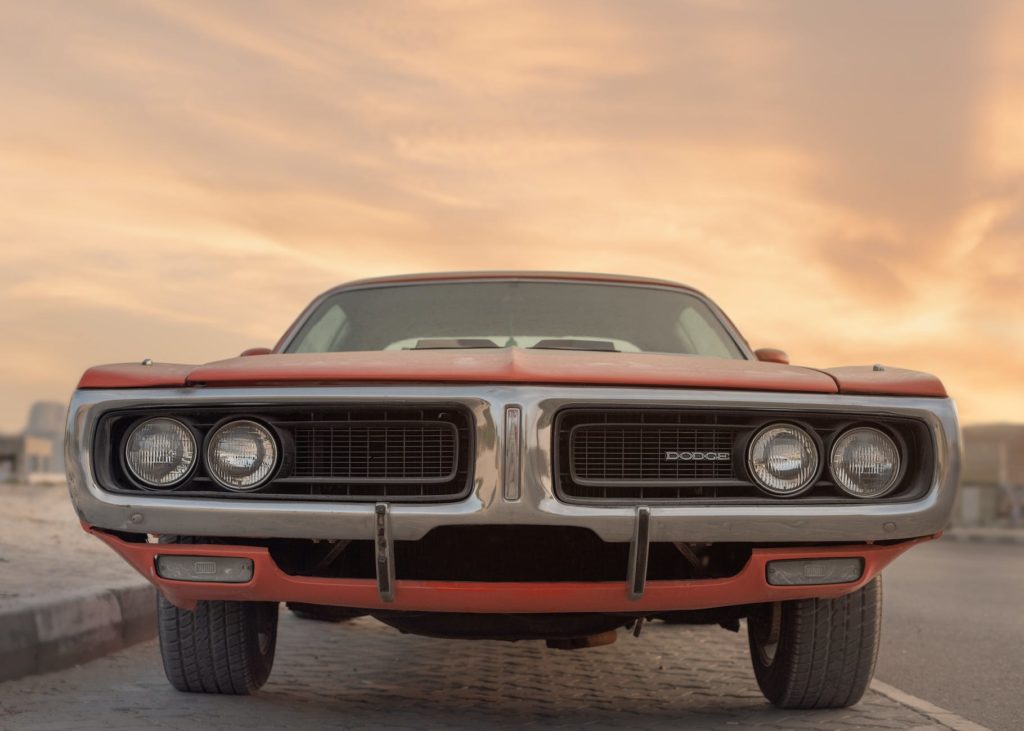
Potrzeby sektora motoryzacyjnego są nieustannie rosnące, a wraz z nimi wzrasta zapotrzebowanie na wysokiej jakości rozwiązania kablowe. Wytwarzanie takich rozwiązań jest kluczowe dla sprawnego działania pojazdów i bezpieczeństwa kierowców. Dlatego coraz więcej firm specjalizuje się w produkcji innowacyjnych kabli, które spełniają najwyższe standardy branżowe. Przy wykorzystaniu zaawansowanych technologii i materiałów, te nowoczesne rozwiązania przyczyniają się do optymalizacji pracy systemów elektrycznych samochodów oraz minimalizują ryzyko awarii.
Kluczowa rola kabli i przewodów w przemyśle samochodowym – bezpieczeństwo i innowacja
Wytwarzanie rozwiązań kablowych dla sektora motoryzacyjnego odgrywa kluczową rolę w zapewnianiu bezpieczeństwa oraz innowacji. Kablami i przewodami jesteśmy otoczeni niemal wszędzie w pojazdach, od układu elektrycznego po systemy komunikacji i sterowania. Bez nich nie byłoby możliwe funkcjonowanie wielu podstawowych elementów samochodu.
Jednym z najważniejszych aspektów produkcji kabli dla sektora motoryzacyjnego jest bezpieczeństwo. Wysoka jakość materiałów używanych do produkcji kabli ma ogromne znaczenie, ponieważ niesprawny kabel może prowadzić do poważnych awarii lub nawet zagrożeń dla życia kierowcy i pasażerów. Dlatego producenci skupiają się na stosowaniu najwyższej jakości izolacji, która chroni przed uszkodzeniami mechanicznymi oraz zapobiega ewentualnym zwarciom.
Innowacje są również istotną częścią procesu produkcyjnego. Wraz z rozwojem technologii motoryzacyjnej, wymagania dotyczące kabli stają się coraz bardziej zaawansowane. Nowoczesne pojazdy wyposażone są w coraz więcej systemów elektronicznych, takich jak kamery cofania, asystent parkowania czy systemy bezpieczeństwa. Wytwarzanie kabli musi być dostosowane do tych nowych technologii i zapewniać nie tylko funkcjonalność, ale także wydajność i trwałość.
W branży motoryzacyjnej istnieje wiele technologii produkcji kabli, które ewoluowały na przestrzeni lat. Od tradycyjnych metod ręcznego skręcania przewodów po automatyczne linie produkcyjne z robotami wspomagającymi proces tworzenia kabli. Zaawansowane rozwiązania technologiczne pozwalają na szybszą produkcję przy zachowaniu wysokiej jakości oraz dokładności wymaganej przez sektor motoryzacyjny.
Jednym z najnowszych trendów w produkcji kabli dla sektora motoryzacyjnego jest stosowanie materiałów o wysokiej wytrzymałości. Nowoczesne samochody wymagają coraz większej ilości energii elektrycznej do napędzania różnych systemów, dlatego ważne jest, aby kable były w stanie przenosić duże natężenie prądu bez ryzyka uszkodzenia lub przegrzewania się. Materiały takie jak miedź lub aluminium są powszechnie używane ze względu na swoją doskonałą przewodność elektryczną.
Wraz z rosnącymi wymaganiami dotyczącymi kabli w przemyśle motoryzacyjnym, kontrole jakości odgrywają kluczową rolę w procesie produkcji. Producent musi zapewnić, że każdy kabel spełnia określone normy i standardy bezpieczeństwa. Kontrole jakości obejmują testowanie wytrzymałości mechanicznej kabla, sprawdzanie izolacji oraz pomiar parametrów elektrycznych. Dzięki temu można mieć pewność, że produkowane rozwiązania są nie tylko innowacyjne, ale także bezpieczne dla użytkowników pojazdów.
Technologie produkcji kabli w branży motoryzacyjnej – od tradycyjnych do zaawansowanych rozwiązań
Branża motoryzacyjna stale się rozwija i wprowadza nowe technologie również w dziedzinie produkcji kabli. Tradycyjne metody ręcznego skręcania przewodów zostały zastąpione przez bardziej zaawansowane rozwiązania oparte na automatyzacji procesu produkcyjnego.
Jedną z najpopularniejszych technologii stosowanych obecnie jest wtryskiwanie tworzyw sztucznych. Proces ten polega na umieszczeniu miedziennych rdzeni przewodów w formach plastikowych i następnie ich pokryciu odpowiednim materiałem izolacyjnym. Wtryskiwanie tworzyw sztucznych pozwala na szybką i precyzyjną produkcję kabli o różnej długości i kształcie.
Innym zaawansowanym rozwiązaniem jest tworzenie kabli wielordzeniowych. Ten proces polega na łączeniu kilku przewodów w jeden, co pozwala na zmniejszenie ilości miejsca zajmowanego przez kable oraz ułatwia instalację w samochodzie. Kablami wielordzeniowymi można zastąpić wiele pojedynczych przewodów, co prowadzi do uproszczenia układu elektrycznego pojazdu.
Kolejną technologią wartą uwagi jest wytwarzanie elastycznych kabli. Elastyczne przewody są niezwykle przydatne w przypadku systemów, które wymagają częstych ruchów lub skręcania, takich jak np. podgrzewane fotele czy regulowane lusterka boczne. Dzięki zastosowaniu specjalnych materiałów izolacyjnych, elastyczne kable są odporne na uszkodzenia mechaniczne i zapewniają niezawodność działania nawet przy intensywnym użytkowaniu.
Wraz z postępem technologicznym branży motoryzacyjnej możemy spodziewać się jeszcze bardziej innowacyjnych rozwiązań produkcyjnych dla sektora kablowego. Automatyzacja procesu produkcji, zastosowanie nowych materiałów izolacyjnych oraz rozwój technologii wtryskiwania tworzyw sztucznych to tylko niektóre z trendów, które będą miały wpływ na produkcję kabli dla sektora motoryzacyjnego.
Materiały stosowane w produkcji kabli – wytrzymałość i efektywność energetyczna
Wybór odpowiednich materiałów jest kluczowy dla zapewnienia wysokiej jakości i trwałości kabli produkowanych dla sektora motoryzacyjnego. Materiały muszą być odporne na uszkodzenia mechaniczne, a jednocześnie efektywne pod względem przewodzenia energii elektrycznej.
Miedź jest jednym z najpopularniejszych materiałów używanych do produkcji kabli samochodowych. Jest to doskonały przewodnik elektryczny o wysokiej wytrzymałości mechanicznej. Kable miedziane są również elastyczne, co ułatwia ich instalację w pojazdach o skomplikowanym układzie elektrycznym.
Innym powszechnie stosowanym materiałem jest aluminium. Choć ma ono nieco gorsze właściwości przewodzące niż miedź, to nadal znajduje szerokie zastosowanie ze względu na swoją lekkość i niską cenę. Aluminium jest często używane do produkcji kabli o mniejszej mocy, takich jak np. przewody do oświetlenia czy systemów audio w samochodach.
Wraz z rozwojem technologii produkcji kabli dla sektora motoryzacyjnego, pojawiają się również materiały innowacyjne. Przykładem może być włókno szklane, które charakteryzuje się wysoką wytrzymałością mechaniczną i odpornością na uszkodzenia chemiczne. Włókna szklane są stosowane głównie w kablach światłowodowych, które znajdują zastosowanie w coraz większej liczbie nowoczesnych pojazdów.
Polimery termoplastyczne to kolejna grupa materiałów używanych do produkcji kabli samochodowych. Polimery te charakteryzują się dużą elastycznością oraz odpornością na działanie czynników atmosferycznych i chemikaliów. Szerokie spektrum dostępnych polimerów umożliwia producentom dobór odpowiedniego materiału do konkretnego zastosowania.
Zapewnienie jakości i zgodności – kontrole jakości w procesie produkcji
Kontrole jakości odgrywają kluczową rolę we wszystkich etapach procesu produkcyjnego kabli dla sektora motoryzacyjnego. Zapewnienie wysokiej jakości produktu jest niezbędne, aby spełnić wymagania klientów oraz normy bezpieczeństwa.
Jednym z podstawowych aspektów kontroli jakości jest testowanie wytrzymałości mechanicznej kabla. Przewody muszą być odporne na uszkodzenia spowodowane np. naciąganiem czy ścieraniem. Testy obejmują m.in. badanie odporności na zginanie, rozciąganie i ściskanie kabla.
Kolejnym ważnym elementem kontroli jakości jest sprawdzanie izolacji. Izolacja ma za zadanie chronić przewody przed zwarciami oraz zapobiegać przenikaniu wilgoci i innych czynników zewnętrznych do wnętrza kabla. Testy izolacji polegają na sprawdzeniu jej grubości, elastyczności oraz zdolności do utrzymania odpowiedniego poziomu izolacyjności elektrycznej.
Pomiary parametrów elektrycznych to kolejny istotny etap w procesie kontroli jakości produkcji kabli dla sektora motoryzacyjnego. W ramach tych testów sprawdzane są takie parametry jak opór przewodu, pojemność kondensatorowa czy indukcyjność magnetyczna. Prawidłowe wartości tych parametrów są kluczowe dla prawidłowego działania układu elektrycznego pojazdu.
Ekologiczne aspekty wytwarzania kabli – zrównoważony rozwój w przemyśle samochodowym
Wytwarzanie kabli dla sektora motoryzacyjnego wiąże się również z dbałością o środowisko naturalne. Przemysł samochodowy coraz bardziej skupia się na zrównoważonym rozwoju i redukcji negatywnego wpływu na środowisko.
Jednym ze sposobów, aby ograniczyć negatywne skutki produkcji kabli, jest recykling materiałów. Wiele firm zajmujących się produkcją kabli stosuje procesy recyklingu, które umożliwiają odzyskanie surowców i ich ponowne wykorzystanie. Dzięki temu zmniejsza się ilość odpadów oraz zużycie surowców naturalnych.
Kolejnym aspektem ekologicznym jest minimalizacja zużycia energii w procesie produkcyjnym. Producentom zależy na tym, aby jak najbardziej efektywnie wykorzystać dostępne źródła energii oraz ograniczyć emisję gazów cieplarnianych. Stosowanie nowoczesnych technologii produkcji pozwala na osiągnięcie większej efektywności energetycznej.
Ostatnim ważnym aspektem ekologicznym jest walidacja produktu pod kątem substancji niebezpiecznych. Kablami są otoczone różne elementy pojazdu, dlatego ważne jest, aby były one wolne od substancji szkodliwych dla zdrowia człowieka i środowiska. Produkcja kabli musi spełniać odpowiednie normy i standardy dotyczące substancji niebezpiecznych.
Rozwój i innowacje w produkcji kabli dla pojazdów elektrycznych – nowe wyzwania i perspektywy
Wraz z rosnącym zainteresowaniem pojazdami elektrycznymi, produkcja kabli dla tego sektora staje się coraz bardziej istotna. Pojazdy elektryczne wymagają specjalistycznych rozwiązań kablowych ze względu na swoje unikalne potrzeby.
Jednym z głównych wyzwań jest wysoka moc przenoszona przez kable. Samochody elektryczne wymagają znacznie większej ilości energii niż tradycyjne samochody spalinowe. Kablami muszą być w stanie przewodzić duże natężenie prądu bez ryzyka uszkodzenia lub przegrzewania się. Dlatego stosuje się materiały o wysokiej przewodności, takie jak miedź czy aluminium.
Innym aspektem jest minimalizacja strat energetycznych. W przypadku samochodów elektrycznych każda strata energii ma duże znaczenie dla efektywności działania pojazdu. Kablami muszą być zaprojektowane tak, aby minimalizować straty energetyczne podczas przewodzenia prądu elektrycznego.
Wraz z rozwojem technologii samochodów elektrycznych pojawiają się również innowacje w produkcji kabli. Producentom zależy na tworzeniu bardziej wydajnych i lekkich kabli, które jednocześnie spełniają wszystkie wymagania dotyczące bezpieczeństwa i trwałości. Nowoczesne materiały izolacyjne oraz zaawansowane technologie produkcyjne pozwalają na osiągnięcie tych celów.
Dostosowanie się do zmieniających się potrzeb rynku – produkcja kabli a trendy w przemyśle motoryzacyjnym
Rynek motoryzacyjny jest dynamiczny i stale ewoluuje, co wpływa również na produkcję kabli dla tego sektora. Producenci muszą dostosowywać swoje procesy produkcyjne do nowych trendów oraz rosnących oczekiwań klientów.
Jednym z obecnych trendów jest wzrost znaczenia systemów autonomicznych. Samochody wyposażone w takie systemy wymagają większej ilości sensorów i komponentów elektronicznych, co prowadzi do wzrostu zapotrzebowania na odpowiednie rozwiązania kablowe. Produkcja musi uwzględniać te nowe potrzeby i dostarczać innowacyjne rozwiązania, które spełniają wymagania systemów autonomicznych.
Kolejnym trendem jest elektryfikacja pojazdów. Coraz więcej samochodów na rynku jest hybrydowych lub w pełni elektrycznych. Wytwarzanie kabli dla tych pojazdów wiąże się z koniecznością zapewnienia odpowiedniej wytrzymałości oraz przewodzenia energii elektrycznej. Produkcja musi uwzględniać specyficzne wymagania dotyczące kabli dla pojazdów elektrycznych.
Ostatnim trendem wartym uwagi jest rozwój technologii komunikacji. Samochody są coraz bardziej połączone z siecią, co prowadzi do wzrostu zapotrzebowania na zaawansowane rozwiązania kablowe umożliwiające szybką transmisję danych. Produkcja musi dostosować się do tych zmian i oferować odpowiednie kable komunikacyjne, które spełniają najnowsze standardy.